Engineering & Constructing Wood Substrates
Wood is NOT wood, is NOT wood, is NOT wood!!! The use of wood-based substrates (or wood components in peat-based substrates has to evolve since the 1990’s when products were first developed and commercialized in Europe. It was not until 2004-2005 that research began here in the United States on using these materials as a component in horticultural substrates. Since 2004 there has been a growing interest in the use of wood materials in substrates. At no time has the potential been greater for the inclusion of these materials into our current greenhouse and nursery substrates than now. With interest and opportunity comes the need for understanding the differences in these products/materials and an even greater need for a systematic understanding of how wood components are manufactured and used. Among the many aspects of our substrate research program here at NCSU, it is our aim to provide the analysis and characterization of wood substrate components so that accurate nomenclature of these products can be better understood and used when describing wood materials.
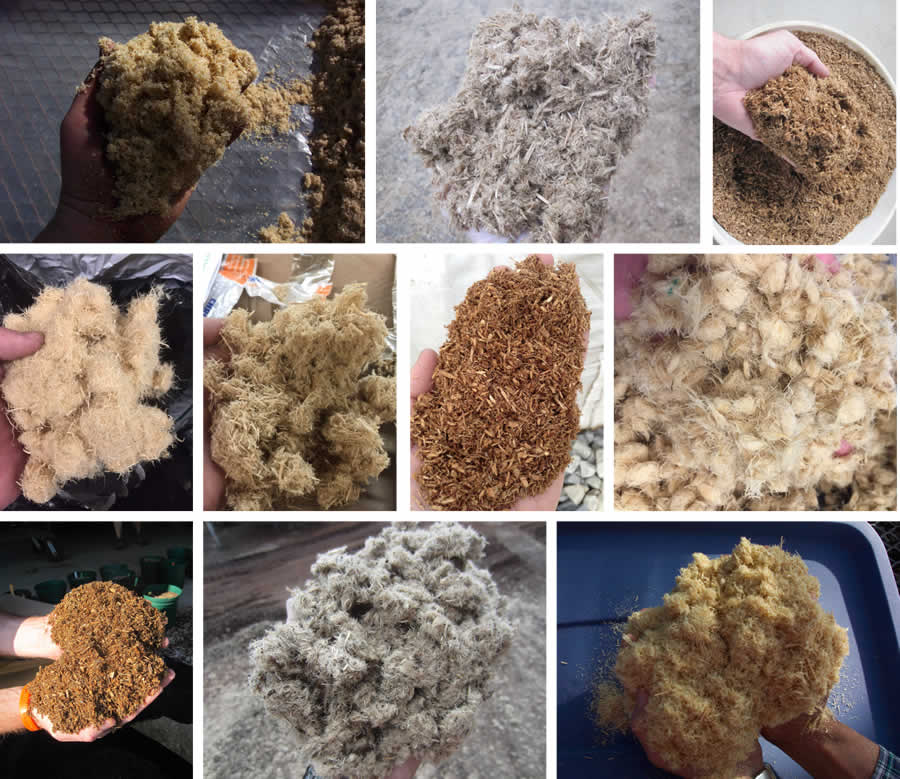
Wood Component Production
There are many ways to produce wood components, and there are even more factors that influence the consistency and reproducibility of those components during processing. There are many types of machines that reduce trees/logs into smaller sizes (comminution); shredders, chippers, wood hogs, shavers, etc. There are also different techniques and machinery used to further reduce those smaller wood materials (feedstock) into various types of wood components. No two types or methods will yield the exact same end-product. Regardless of the type of machine/machinery used, the variables that influence the engineering of the wood components have to be understood, accounted for, and minimalized as much as possible. As with all things “Engineered,” there are standards, protocols, and guidelines for how to successfully reproduce a consistent product. These principles also apply to the manufacturing of wood materials.
Tree Harvesting
Tree harvesting equipment and machinery used to reduce the trees/logs to smaller sizes can range in size and shape. The figure on the left shows a “chipping” operation and on the right a “shredding” operation. Initial comminution of trees is an important variable in how to process specific wood components.
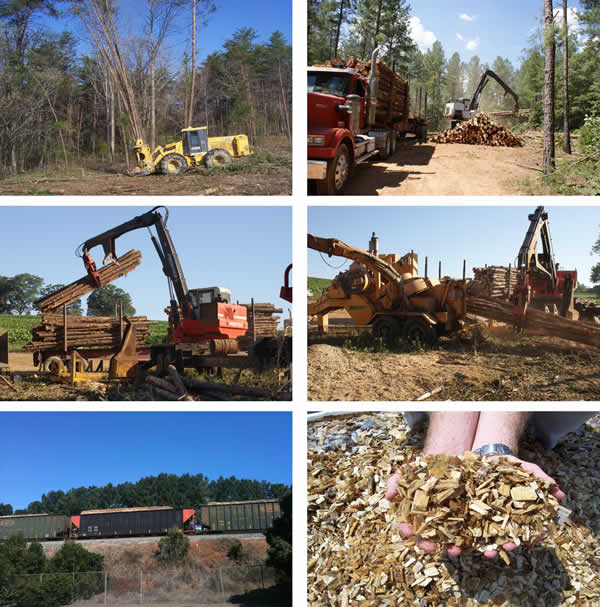
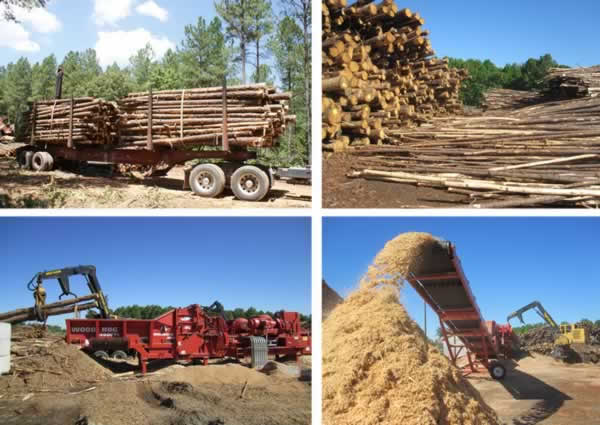
Chipped feedstock examples
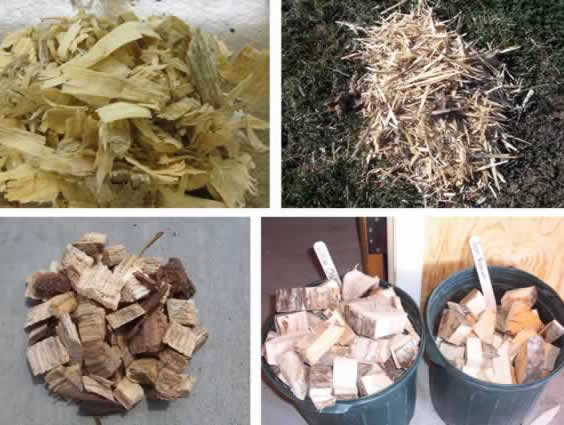
Shredded feedstock examples
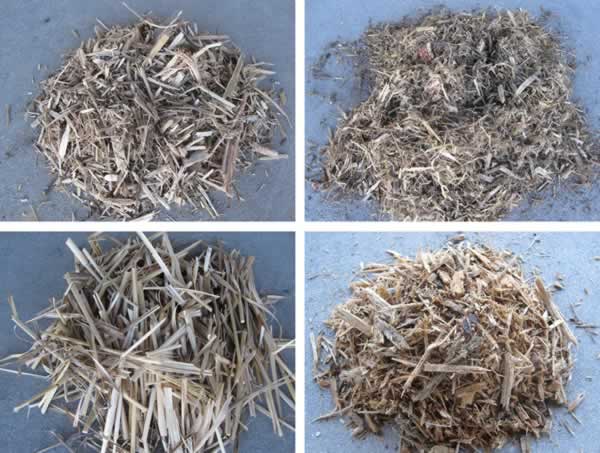
Feedstock Differences
Differences in feedstock size and shape (as a result of the machinery used to grind it) will inevitability effect the type of wood fiber or wood ship component produced. All of the wood components in the photo above were trees of the same age, harvested at the same time, but initially processed using different equipment which yielded different feedstocks. All feedstocks were then hammer milled at the same moisture content, through the same screen size, and at the same feed rate yet the end-products are very different and would have different properties when mixed with peat in a substrate.
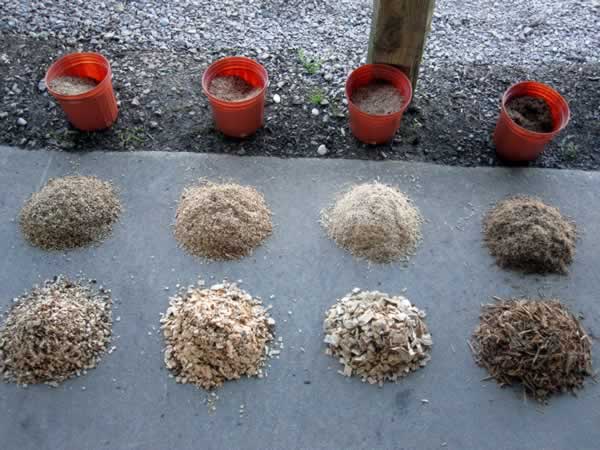
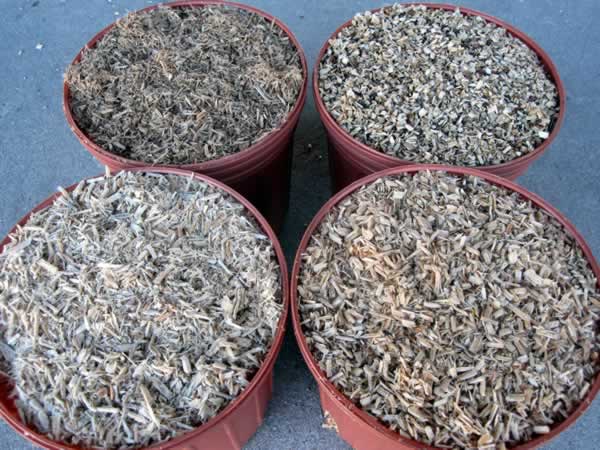
Processing Feedstock
Hammer mills, twin-rotating discs, since and double screw extruders are some of the machine types used to further process wood feedstocks into the final product (substrate component).
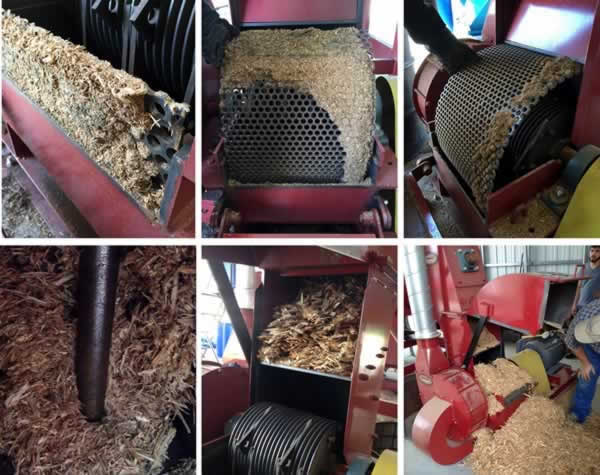
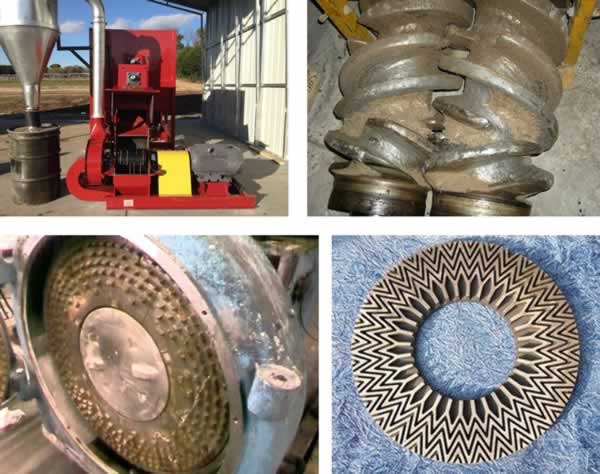
Storage
Storage of trees, processed trees, wood feedstocks, and processed end-products (wood substrate components) can be critically important. Whether materials are stored outdoors or indoors (covered) depends on the need for controlling the moisture content of the materials. Depending on the type of machine and technique used for making wood substrate components, moisture control is essential! Moisture is the key factor in quality control for processing wood materials (and any other organic material for that matter). The moisture content not only influences the grinding/processing of the wood feedstocks but it also plays a role in the storage quality and shipping weight of the end-products.
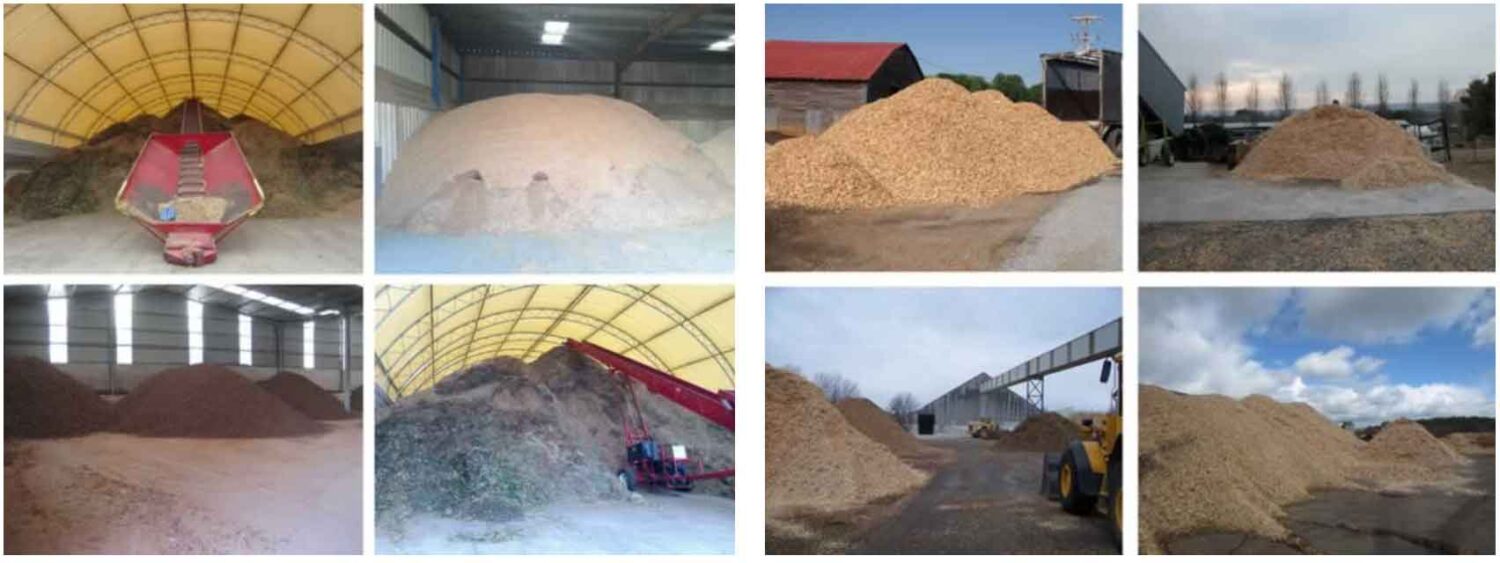
Moisture Content
Moisture content, being the main variable in consistently producing wood/organic materials can not only change the particle size of the end-products but can clog the screens of hammer mills (leading to burning up and destroying the motors) as seen in the photos above and it can change the volume of material processed through the mill. The volume of the end-product coming out of a hammer mill will be larger than the volume of feedstock put in the mill. The volume of product depends on feedstock size and screen size (among other things). Moisture does not play such a significant role in other processing techniques but it does with hammer mill processing.
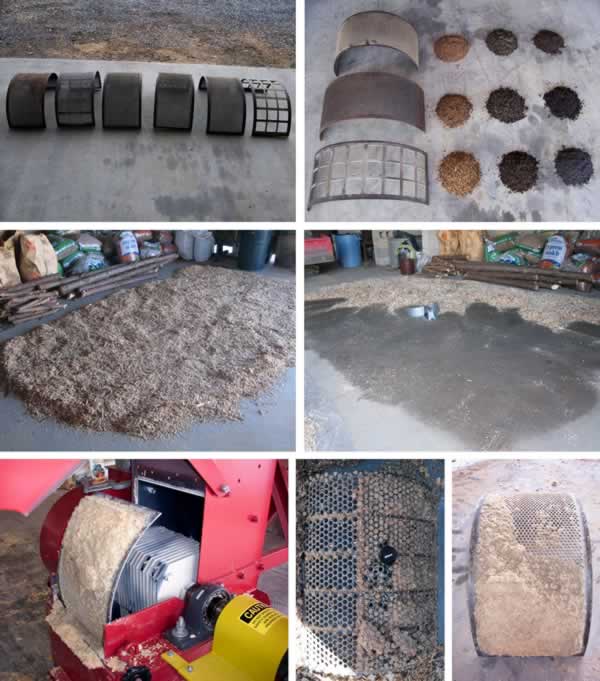
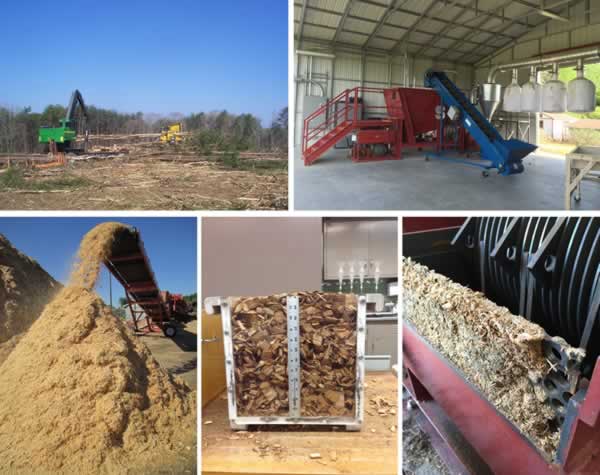
Other Considerations
Other considerations in the processing of trees is the variability in feedstocks/wood chips as seen in the photos below. Trees fed into this chipper yielded chips and shreds of many different shapes, sizes, and thicknesses. The variability of those wood materials can greatly influence how they are processed in a hammer mill. Shreds process differently than chips, and larger pieces process differently than smaller ones, potentially yielding an inconsistent and unreproducible end-product. The age of harvested and stored trees (four photos to the right) can also influence wood substrate production and visible characteristics. The discoloration comes from the initial fungi that inhabit trees.
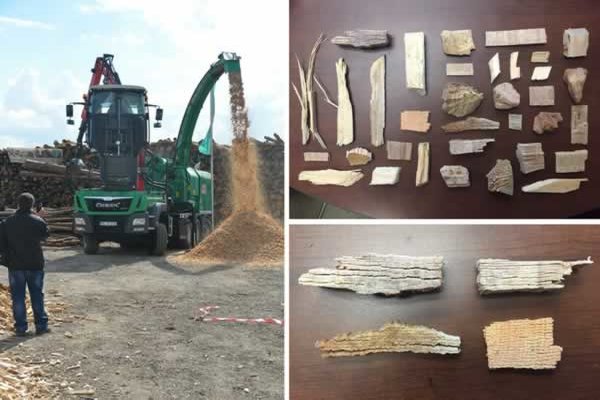
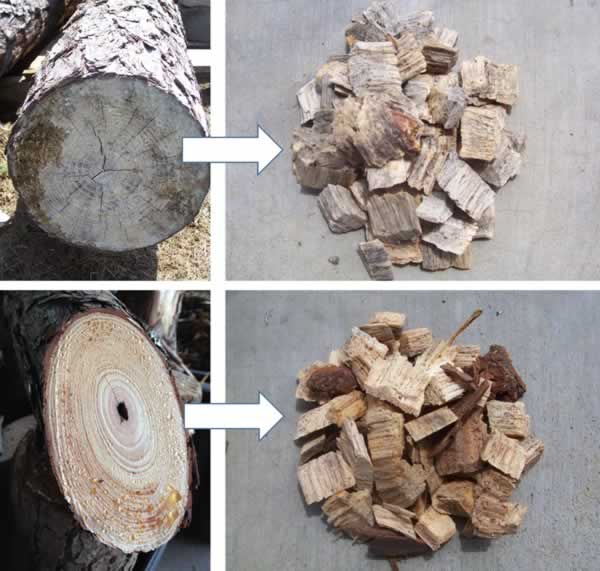
Coloring
The coloring of wood substrates/components is one aspect of production and commercialization that can be, and in many cases is, very important relative to the usability and acceptance of these new products. Substrate manufacturers, distributors, and growers expect “soil to be brown/dark”. Peat moss and pine bark have no issues with color but the blond wood components are visibly much different. Methods of coloring wood chips during, or after, products have been developed and tested so that the end-product is more traditional and “soil-like”.
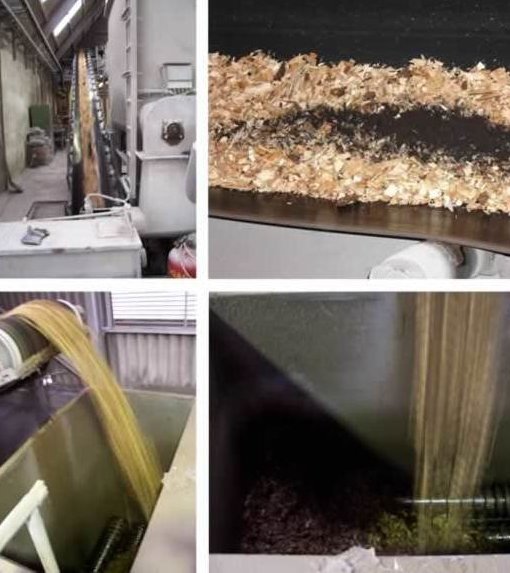
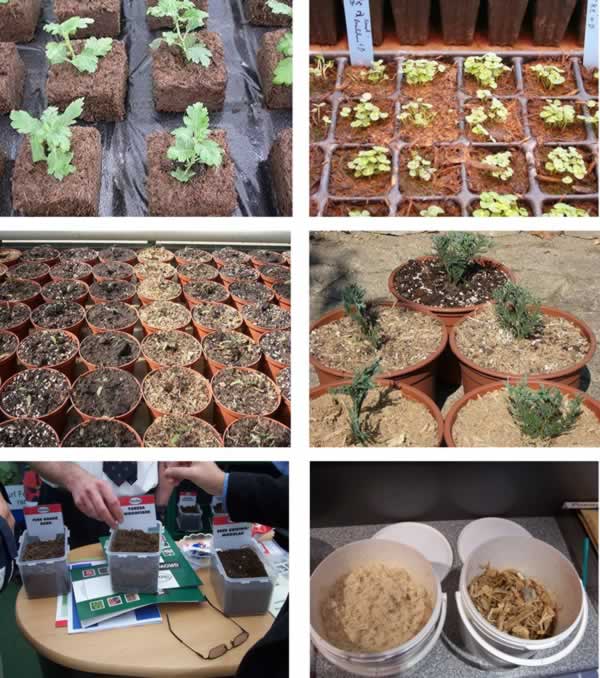
Wood Sources
Many tree species and wood sources have been investigated over the years as potential substrates/components. The main species used to make commercial products are Pinus, Larix, and Picea. Other species (nine photos on the right side above) show some of the many other species tested. Factors that influence the ability of a particular tree species (or wood source) include availability, an abundance of resources, other competing markets for the trees, the toxicity of wood, rate of degradation and breakdown, grind-ability and or process-ability, etc.
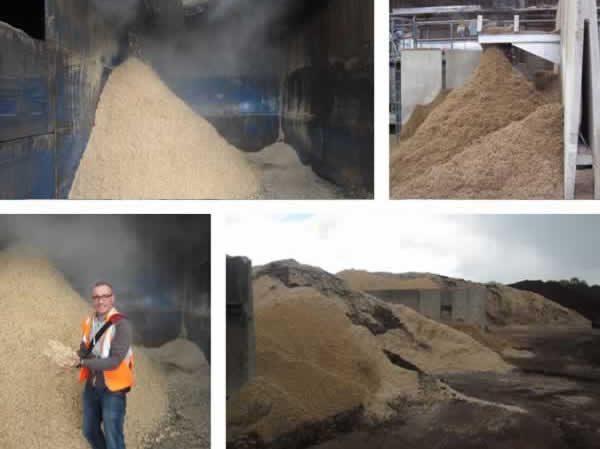
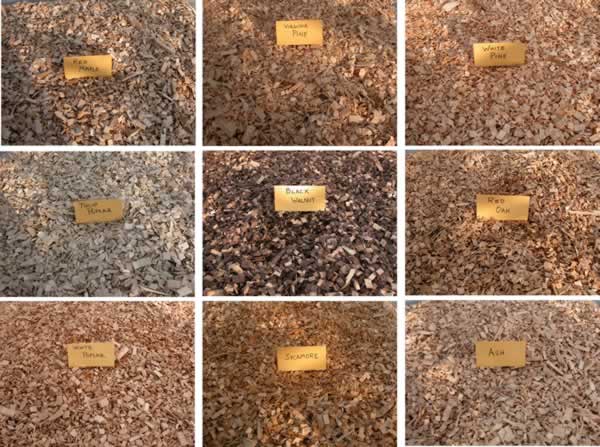
Incorporating Wood Sources
Once produced, the incorporation of wood components into peat moss or pine bark is the next important step to consider and address. Depending on the type and amount of fiber, blending may not be the same as traditional peat: perlite substrates. If engineered properly, substrates with wood fiber/chip components should work fine in current grower operations and machinery. However, there may be a need to modify certain practices (depending on the percent of wood in the mix).
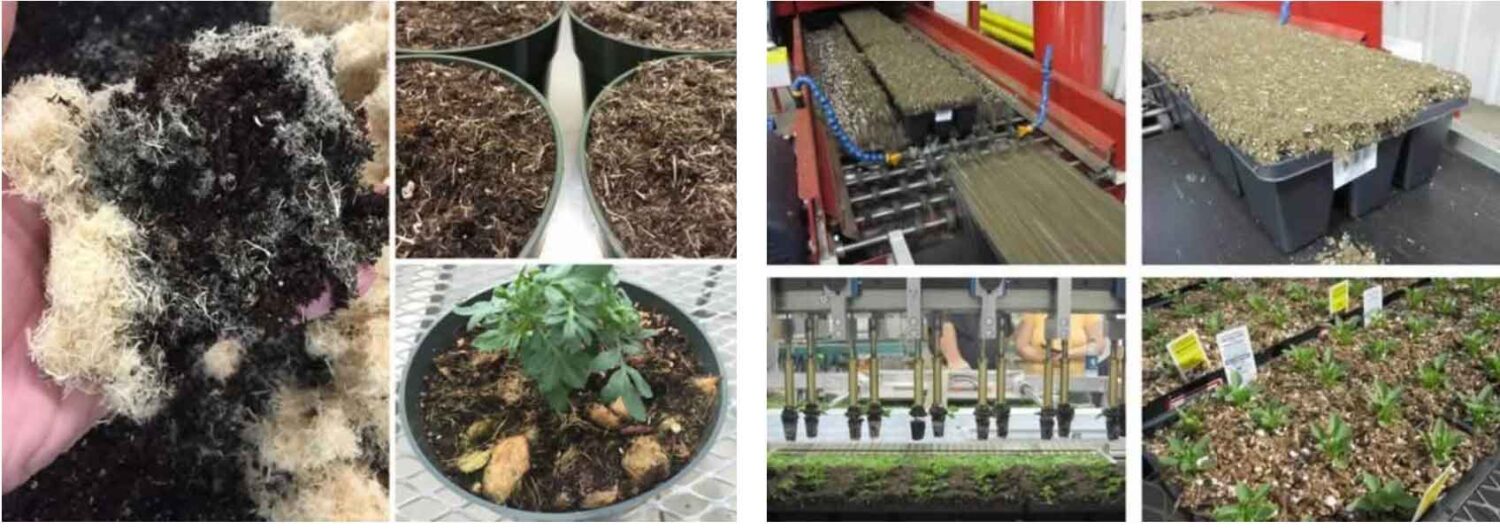
Engineering Materials
The engineering of wood and bark materials is one of the main objectives and areas of focus for the Substrate Science research group here at NC State. While much has been learned, there is much more that needs to be done to facilitate the commercialization, acceptance, and use of these new products. Researchers in the United States and around the world are working and collaborating on the research and development of these diverse materials.
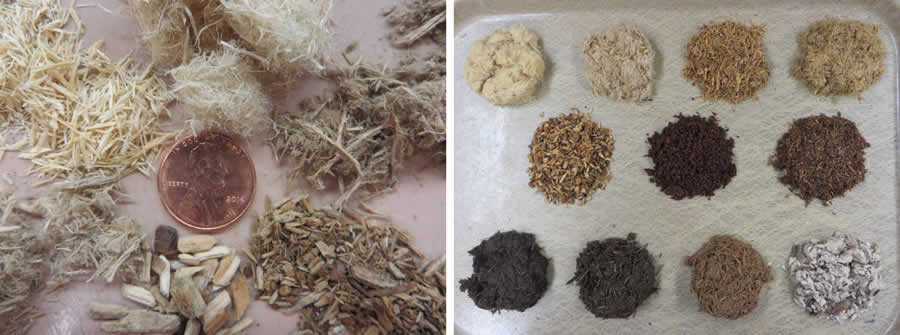
Wood is NOT Wood!
Just as we know very well….peat is NOT peat, is NOT peat…..we must also learn and appreciate that wood is NOT wood, is NOT wood! The range of peat materials, fractions, sizes, and ages is extremely diverse and these different peats are used in different ways. The same mindset is needed when working with wood components
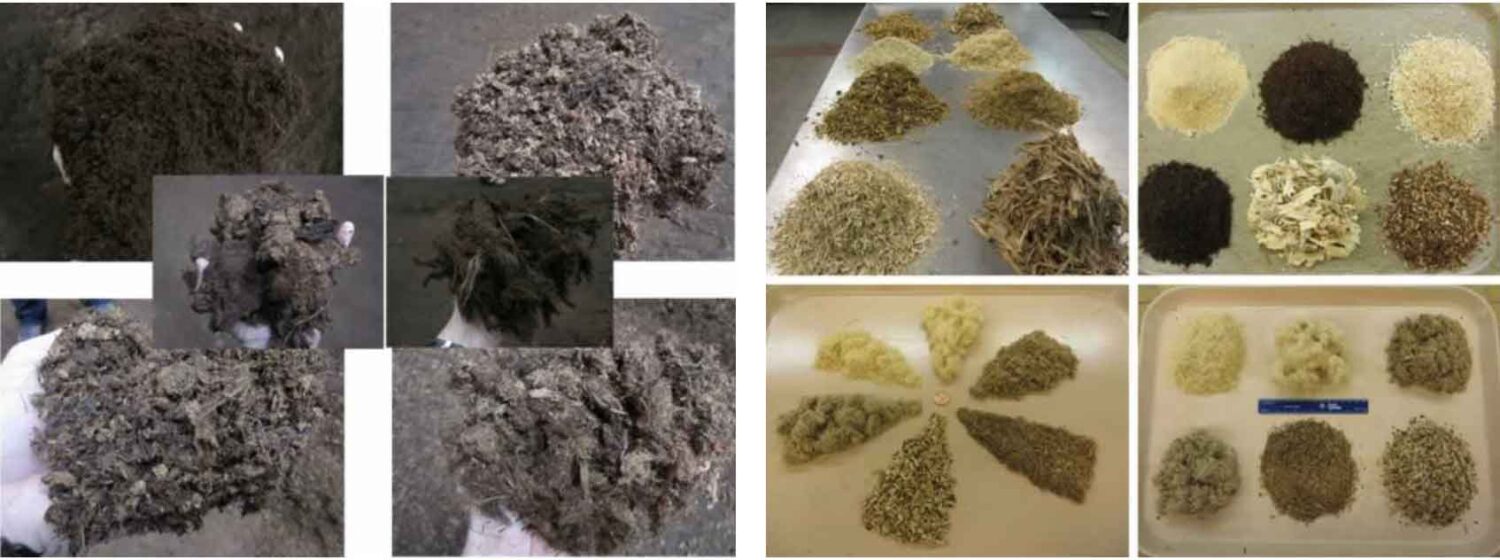